Clean Technology
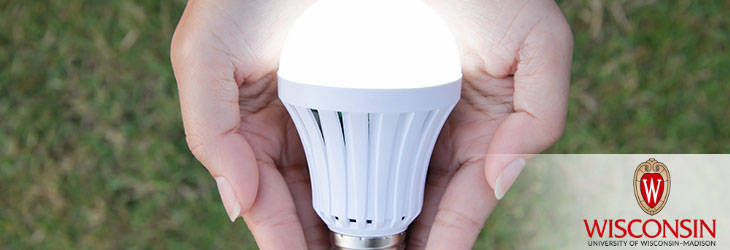
Improved Biomass Conversion with GVL Co-Solvent
WARF: P150223US01
Inventors: James Dumesic, Ali Hussain Motagamwala
The Wisconsin Alumni Research Foundation (WARF) is seeking commercial partners interested in developing a method for producing biomass-derived sugars using a cost-saving solvent mixture.
The use of aromatic compounds as co-solvents with gamma-valerolactone results in enhanced production and separation of C5 and C6 carbohydrates, and dehydration products.
Overview
Production of fuels and chemicals from biomass requires utilization of all biomass fractions, i.e., cellulose, hemi-cellulose and lignin. Thus, product molecules from all fractions of biomass must be produced at high yields to minimize the feedstock cost, and at high concentrations to minimize separation costs.
Catalysis expert James Dumesic and his lab previously pioneered a method for producing soluble carbohydrates from biomass using a polar aprotic solvent, gamma-valerolactone (80-90% GVL with 0.5% sulfuric acid). This process produces hydrolysate with high carbohydrate yields, and high sugar concentrations (>12 wt%) can be obtained after separation of the solvent from the hydrolysate using liquid CO2. The used GVL may be recycled to improve the economic viability of the process.
Prof. Dumesic’s team has shown that GVL-based dilute acid hydrolysis can be cost competitive with the National Renewable Energy Laboratory’s (NREL) process for bioethanol production, and they continue to pursue process improvements.
Catalysis expert James Dumesic and his lab previously pioneered a method for producing soluble carbohydrates from biomass using a polar aprotic solvent, gamma-valerolactone (80-90% GVL with 0.5% sulfuric acid). This process produces hydrolysate with high carbohydrate yields, and high sugar concentrations (>12 wt%) can be obtained after separation of the solvent from the hydrolysate using liquid CO2. The used GVL may be recycled to improve the economic viability of the process.
Prof. Dumesic’s team has shown that GVL-based dilute acid hydrolysis can be cost competitive with the National Renewable Energy Laboratory’s (NREL) process for bioethanol production, and they continue to pursue process improvements.
The Invention
Building on their work, the researchers have now developed a process that utilizes an inexpensive co-solvent to replace a fraction of the GVL and also facilitates the separation of the organic solvents from the hydrolysate. Furthermore, the separated aqueous solution, rich in carbohydrates, contains a negligible amount of dissolved lignin.
The new method uses a relatively inexpensive solvent mixture, which also minimizes the separation cost. This improves the economic potential and additionally provides a valuable feedstock for production of aromatics (from lignin). This new improvement offers the opportunity to develop an economically viable process that combines catalytic lignin upgrading and carbohydrate production from biomass. The co-solvent mixture can be tailored for the production of C5 and C6 carbohydrates or degradation products such as furfural.
The new method uses a relatively inexpensive solvent mixture, which also minimizes the separation cost. This improves the economic potential and additionally provides a valuable feedstock for production of aromatics (from lignin). This new improvement offers the opportunity to develop an economically viable process that combines catalytic lignin upgrading and carbohydrate production from biomass. The co-solvent mixture can be tailored for the production of C5 and C6 carbohydrates or degradation products such as furfural.
Applications
- Biomass depolymerization and conversion
- Biofuel/bioproduct industries; cellulosic ethanol plants
Key Benefits
- High commercialization potential
- Effective, industry-viable and sustainable
Stage of Development
In an experiment using corn stover, more than 95% of the polysaccharides were recovered as known soluble products, with C5 and C6 sugar yields at 84% and 79%, respectively. Additionally, lignin precipitated from the solvent and was recovered as a solid phase at the bottom of the separator. The yield of this lignin was 44%. The remaining lignin was present in the organic phase (avoiding problems with lignotoxins should the sugar stream be used for fermentation). The obtained lignin can be used in an integrated process to produce aromatic chemicals that can either be used as a co-solvent in this process or as a drop-in fuel.
Additional Information
Related Technologies
For current licensing status, please contact Mark Staudt at [javascript protected email address] or 608-960-9845